
Wooden Bottoms
The process starts when we get alderwood logs delivered to our factory. The logs are sawn up into different dimensions depending on the model and size of wooden bottom to be produced.
The drying of the wood is the next step. The sawn planks will normally stay around 3 - 4 weeks in our wood drier until the moisture content is reduced to around 11 - 12%. Our new kiln with new drying technology ensures precision, which is important for the stability of shape after machining. The dry planks are then cut up to different lengths according to the size of the bottom.
The unique Troentorp clog bottom with our raised heel and arch support is formed during the milling phase. Extra thick wood and our specially developed forms give our Ideal and Original footbeds their anatomical shape.
After milling, an adhesive is applied to both the wood and the outsole. The wood and outsole is then carefully pressed together.
Then it’s time for fine milling, which is done in our especially developed Hultanäs machines. The nailing groove and the characteristic Troentorp decorative stripe on the heel are then cut out. As a finishing touch, the instep is polished and the outside of the bottom is varnished.
Leather Uppers
We work with many different types of leathers such as vegetable tanned, pull-up, suede, and nubuck. Each type of leather has its own characteristics and our craftsmen and women have to adapt the way they work depending on the leather type.
In this phase, the clicker first inspects each leather hide and then determines what direction to cut the leather in.
Each model and size we provide has its own die to give the best possible fit for the clogs.
After clicking the upper leather, linings and padding are attached and stitched together with the upper. Straps, buckles, and eyelets are then attached before final inspection of the finished uppers.
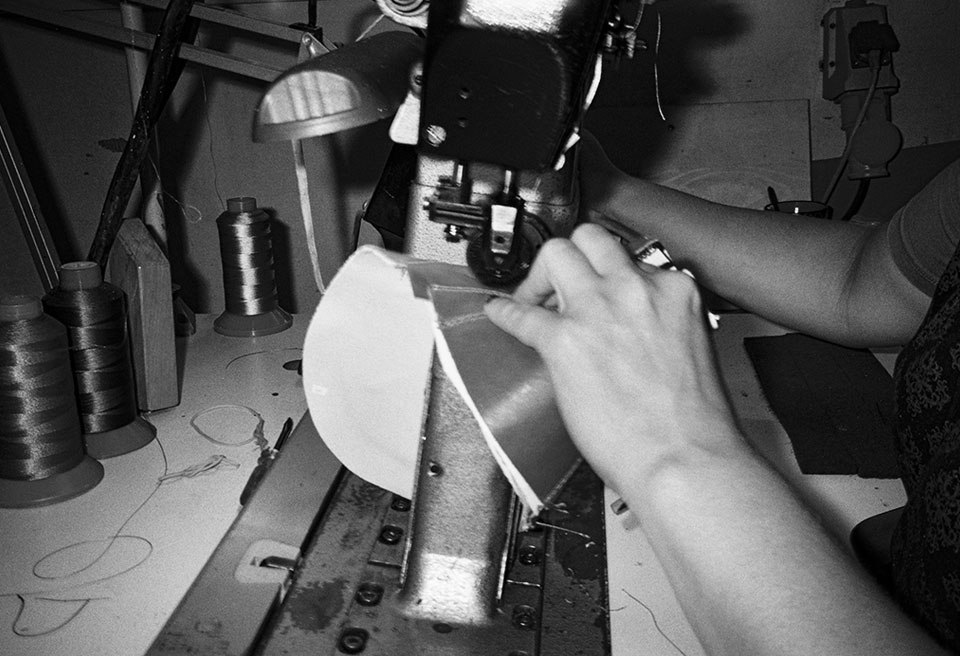
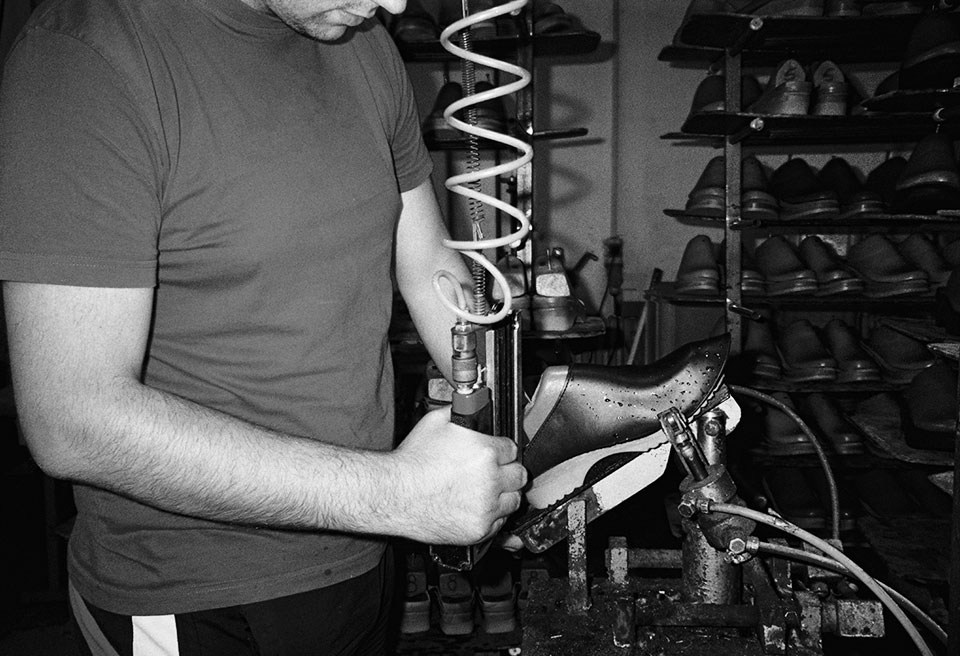
Lasting
The uppers are soaked or steamed to soften the leather fibers before they are stretched onto the last. This way we give the clogs their shape before they get to wearer’s foot.
Unlike most other producers of wooden clogs, at Troentorp we stretch the leather uppers over the last before nailing the clogs. The leather must be treated as a living material and when lasting the shoes one must be careful since the level of stretch in the upper will depend both on the skin that is being used, and where in the skin the upper has been punched out. This is a very important stage in the production since it will ensure the clogs get a good fit and retain their shape.
If you look closely, you can see some small holes on the wooden bottoms. This is because the uppers have been stretched over the last and fastened with staples before the nailing process. These staples are then removed after the clogs have been nailed.
Nailing
The clogs are nailed with real nails rather than staples. This production stage is much more physically demanding than stapling, but the result is our distinctive Troentorp look and quality.
After the clogs have been nailed, the surplus leather is cut away and every clog is carefully checked before entering a drying room. Once dry, the clogs are put to cool down before we remove the lasts.
The clogs are then quality checked, polished and packed.
After that, the Troentorp clogs are ready for you to wear!
